中國汽車動力鋰電池市場規(guī)模不斷擴(kuò)大,并且在全球范圍內(nèi)占據(jù)重要地位,隨著中國政府對環(huán)境保護(hù)和可持續(xù)發(fā)展的重視,推動了新能源汽車市場的快速發(fā)展。政府制定了一系列支持政策,如補(bǔ)貼和減免稅政策,促進(jìn)了新能源汽車的銷售,進(jìn)一步推動了汽車動力鋰電池市場的擴(kuò)大。
動力電池內(nèi)部也是一整個復(fù)雜的系統(tǒng),從電芯、電池模組、電池包,歷經(jīng)一道道制造工序,最后組裝成一整個動力電池系統(tǒng)。這其中,材料與材料、模組與模組、電池包結(jié)構(gòu)的連接就涉及到高要求的焊接工藝——激光焊接。在動力電池生產(chǎn)過程中,電池殼體焊接的質(zhì)量穩(wěn)定性會影響電池組裝系統(tǒng)的一致性和安全性。動力電池殼體內(nèi)部主要包含有機(jī)電解液、特殊隔膜,蓋板上主要包含防爆閥、極柱、安全帽、注液孔等。殼體與蓋板的封口焊接要求很高,其焊接質(zhì)量直接影響電池的密封程度,焊接不良會導(dǎo)致電池漏液、析鋰、電池外觀不達(dá)標(biāo)等問題。當(dāng)前的常規(guī)解決方案是先將殼體和頂蓋進(jìn)行預(yù)焊,然后進(jìn)行滿焊。
滿焊,又稱全焊,意思是在焊接過程中,需要將焊接的兩個部件完全融合成為一個整體。滿焊對焊縫的要求高,需盡可能地使焊接的兩者沒有間隙,以達(dá)到無縫連接的焊接效果。
針對上述的工藝要求,創(chuàng)鑫激光子公司寶辰鑫采用雙光束(環(huán)形光斑)激光器為核心的焊接方案,經(jīng)驗證,各方面工藝都可達(dá)到客戶嚴(yán)格的標(biāo)準(zhǔn)要求。目前,鋁合金材料的電池殼占整個動力電池的90% 以上。動力汽車電池的外殼材料通常采用3003鋁合金,而鋁合金對激光的反射率極高, 激光焊接難度較大,焊接過程中可能會面臨飛濺、爆點、內(nèi)部氣孔、鋁殼變形等各類問題。面對這一問題,寶辰鑫雙光束(環(huán)形光斑)激光器逐個擊破。寶辰鑫雙光束(環(huán)形光斑)激光器,采用環(huán)形光斑設(shè)計,在進(jìn)行動力電池外殼焊接時,可利用光斑較小的內(nèi)環(huán)的高功率密度光斑作用于工件,生成匙孔,獲得足夠的焊接熔深;利用外環(huán)對焊接過程中的熔池提供更多能量以增大焊縫寬度,并延長匙孔閉合時間,幫助熔池氣體逸出,從而降低焊縫氣孔率。
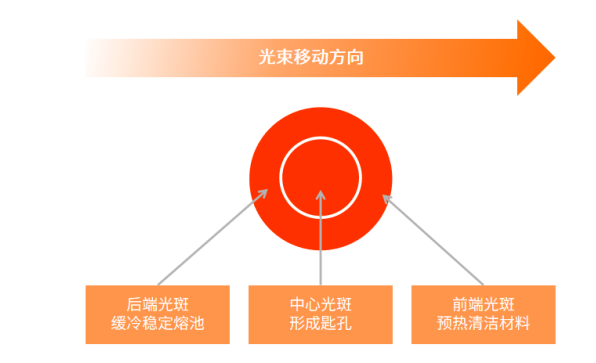
在該焊接項目中,材料頂蓋厚度為2mm,外殼厚度為0.3mm鋁材,需達(dá)到的焊接要求具體為:熔深0.3~0.9mm ,熔寬1.4±0.5mm,余高≤0.2mm。根據(jù)客戶的需求,對材料和應(yīng)用樣品進(jìn)行分析后,整理出焊接方式如下圖所示:
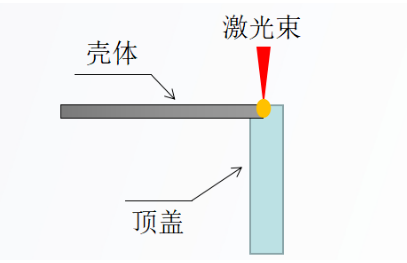
▲焊接示意圖
工程師在以往焊接經(jīng)驗基礎(chǔ)上,對焊接配置進(jìn)行多重驗證后,得出一套最優(yōu)的焊接方案。焊接方案采用寶辰鑫專為行業(yè)研發(fā)的高性能雙光束(環(huán)形光斑)激光器(DBW-2000/2000M),并選配合適的芯徑配比和焊接頭,系統(tǒng)使用寶辰鑫激光焊接系統(tǒng),從而可以得到良好的焊接質(zhì)量。隨著激光技術(shù)的不斷突破和發(fā)展,激光焊接技術(shù)及工藝也將得到更大的提升,并在動力電池制造領(lǐng)域發(fā)揮更大的作用,推動動力電池產(chǎn)業(yè)的高質(zhì)量發(fā)展。